
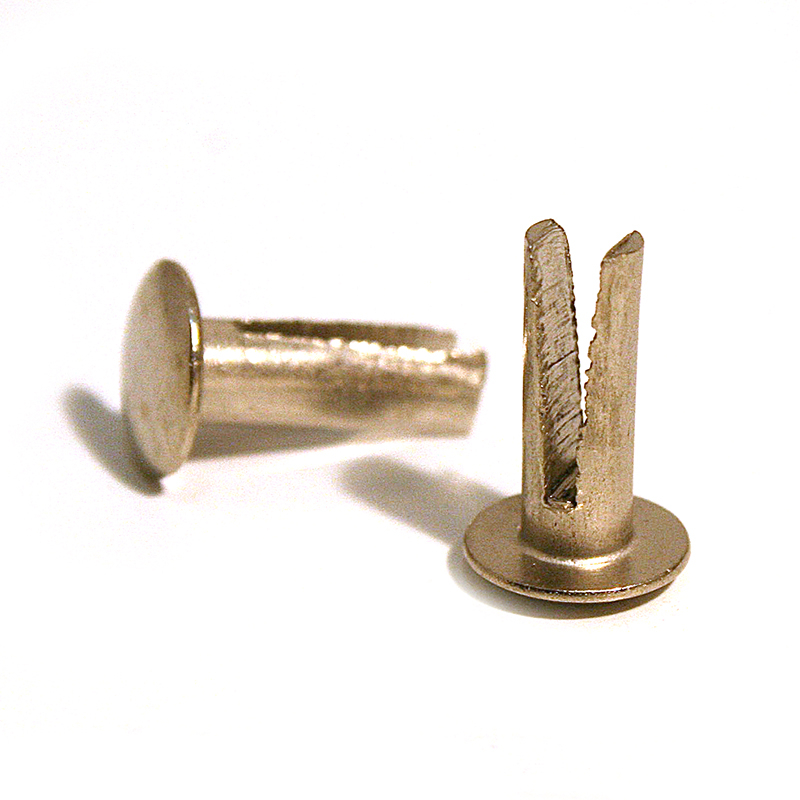
Welding requires extreme heat to melt the parts to be jointed. These joints can be lap joints or butt joints which find application in major structures including boiler shells, automobile flooring in buses, and structural parts in the aerospace industry.įrequently Asked Questions Why is a rivetted joint is common in aircraft joints compared to welding? Leakage may be a problem for this type of joints, but this is overcome by special techniques.ĬonclusionIn a nutshell, a rivet is a structural member which gives permanent joint.Dissimilar metals can also be joined, even non-metallic joints are possible with riveted joints.This rivet may fail in shearing action or in tensile action during the application. Single riveted means one row of the rivet in joint. Sometimes based on joint strengths, triple-riveted are also possible. Types of riveted joints:There are mainly two types of riveted joints, based on the rivet arrangement-īoth joints are also sub-classified into single riveted and double riveted. If the joint is made to make it leakproof, one must use the forging process. Manufacturing of rivets:Rivets are made from rolled bars by the process of cold heading or cold upsetting. The rivet can be heat treated for achieving better material properties as per the requirement of the structure. Rivet must be having a tensile strength of at least 40 MPa and elongation of at least 26 % as per the Indian standard IS:2998-1982/1992.IS-2100-1962 gives the steel rivet specifications which are used in boilers.The only material requirements are ductility, toughness, and hardness.

Sometimes copper, aluminum are used in corrosive environment.Usually rivet is made up of wrought iron or soft steel due to lower hardness which is necessary to have easy deformation during riveting.If diameter of rivet, d = 24 to 48 mm, Clearance, C = 2 mm If diameter of rivet, d = 12 to 24 mm, Clearance, C = 1.5 mm Usually clearance is considered as per following:.Clearance is taken into consideration while riveting because by pressing the application diameter of the rivet is somewhat increased. For riveting parts to be joined are first drilled with the help of a drilling machine.In this riveting process, the tail of the rivet is converted to 'head' which is sometimes called 'shop head'.Cold riveting is used for the structural joints while hot riveting is used to make leakproof joints to handle or store fluids When c cold rivet (for 12 mm diameter) is taken for making riveted joint, the process is known as cold rivetting, on the other hand, if the rivet is hot and the resulting joint is a hot riveted joint (for rivet diameter greater than 12 mm).Equal and opposite force makes rivet to deform and tail part of the rivet is converted to head at the bottom so, the complete rivet is seated in the plates.Rivet heading process is done with the help of forming die and backup die which keep a rivet in between them and by application of force, the rivet is set in the parts to be joined.Rivet and Its heading Process (riveting):
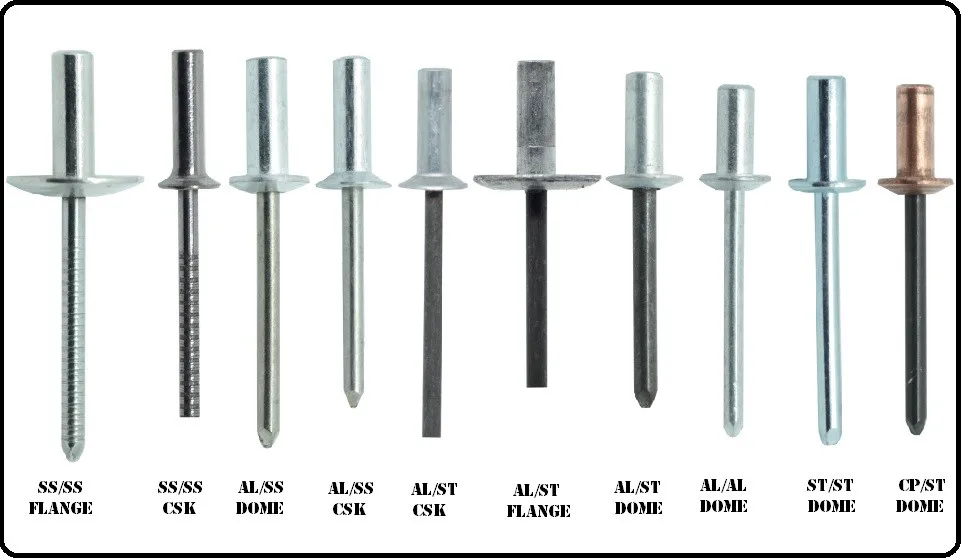
Geometry of rivet In simple language rivet is short cylindrical bar with integral head at top. Definition of riveted joint A riveted joint is a permanent joint with mainly two components (parts to be joined) that are held together by a rivet with the head at the top and the tail at the bottom.
